Logging Systems
Logging From the Ground Up
Whether by horse or helicopter, there are many different ways to cut and organize logs for transportation to timber processing plants.
Horse Logging
Horse logging is not just a relic of the past. It is still being used today. With horse logging, trees are generally felled and bucked by hand with a chainsaw and then skidded by single horses or a team of horses. The horses are equipped with a harness and haul either a single or double tree load, depending on whether using a single horse or a team.
Many horse loggers use a bar with chain hooks attached to it and hook the logs with short chains. Some use small skidding arches, which are basically a set of wheels that get the front of the logs off the ground, increasing the load that a horse can pull. Horse logging is useful on narrow skid trails and in areas that are sensitive, or where the desired stand is too tight to get standard equipment into. Another advantage to horse logging is equipment maintenance. All you need are horseshoes, plus oats and hay for fuel (of course, horses eat a lot when working hard).


conventional Logging
More logs have been moved by conventional logging than any other method in Montana. With conventional logging, trees are felled by hand sawyers and either bucked into logs and limbed in the strip, or tree-length skidded into the landing and then limbed and bucked by hand into logs. After being felled, the trees or logs are skidded with either crawlers or rubber tired skidders that are fitted with skidding winches and arches. The winch is fixed with a long piece of heavy cable that is the mainline. Chokers with sliders are placed on the end of the mainline.
​
The operator backs up to the first log, drops the blade down and sets the brake. Then the winch is put into neutral and the operator pulls the mainline and chokers to the first log. The slider closest to the machine is hooked to the closest log, then the operator goes to the next one and hooks it and so on until the chokers are full. The winch is then engaged and the logs are pulled up to the machine, with the hooked ends suspended off the ground. This makes them easier to pull and causes less soil disturbance.
​
The skidding machine is then driven down to the landing. The logs are unhooked and spread out so the knot bumper or landing man can clean up any limbs and finish bucking them. They are then either decked with the skidding machine or a log loader and hauled by truck to the sawmill.
​
Mechanical Logging
Until the late1980s, logging was mostly completed by conventional and line systems. The felling and bucking of trees was accomplished by chainsaws and stout backs. Then the first de-limbers, grapple skidders and feller-bunchers started showing up in the woods. This greatly changed the dynamics of the timber harvesting community. While reducing the number of loggers in the woods, it created many other jobs outside the logging industry such as equipment mechanics, computer technicians, fuel distributors and equipment salesmen.
With three machines and employees, a mechanical logger could put as much wood in the deck as someone with many more employees working conventionally. The clipper or feller-buncher starts the job by mechanically felling the trees and putting them in piles for skidding. The clipper operator cuts and lays the trees so the skidder can get them out in a safe and efficient manner. The grapple skidder has a hydraulic boom with a grapple that grabs the piles the clipper has cut and lifts up the butts of the trees to minimize soil disturbance.
The skidder operator then drags them to the de-limber (hot logging) or into a deck for the de-limber to work on later (cold decking). The de-limber then grabs the trees, cuts out any rot in the butt and begins to make a log. A boom de-limber has two sets of hydraulic grab arms and two hydraulic saw bars (butt saw and a top saw). The grab arms of the de-limber have knives on both sides, so when the operator extends the boom, the knives cut the limbs off the tree.
A computer tells the operator how far from the butt of the tree the top saw is. When the saw reaches the desired length, the operator hits the top saw button and the tree is cut and ready for loading. The next in line is a log loader and a logging truck. A log truck backs up under the loader, and the loader lifts off the trailer.
The log truck driver then hooks up the trailer tongue, air brakes and trailer lights and puts in the stake extensions. The loader operator then starts putting logs on the truck until it is loaded (typically about 27.5 tons). The truck then heads for the mill, where the logs are turned into lumber products we all use every day.
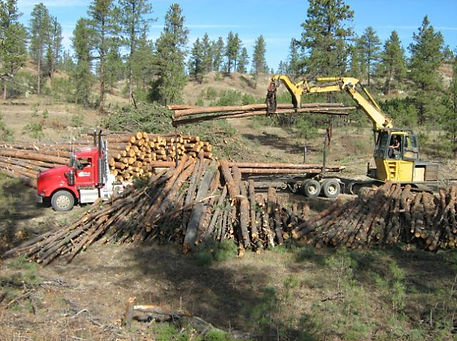

line skidding
Line skidding or "high lead" logging was one of the first mechanical logging methods. The first line machines were actually steam donkeys that were rigged to a spar tree. A steam donkey was a steam engine that ran a series of drums – basically a huge winch. With high lead logging, a logger (in this case, the “high climber") would rig lines into a spar tree sometimes over 100 feet. These high lead systems could skid logs a much longer distance with less effort mainly due to the lift. Without lift, the logs that were being skidded by the ground lead system would get hung up on stumps and rocks.
The modern high lead systems (as pictured) all work on the same basic principle as high lead logging with a steam donkey. The major difference is the spar tree is attached to the machine as the “boom” to get the lift at the machine. Line machines vary from a simple shotgun system which is a two-drum machine with a skyline and mainline, to a "running skyline" which can skid logs up or down hill.
​
When setting up the machine on a strip, a logger must find a nose guy stump to tie the machine back and a tail stump for tying the skyline. The skyline (with a shotgun system) is then pulled down the hill, tied to the tail stump, and pulled tight to get the lift needed to skid the logs. The mainline is attached to the skyline with a carriage which goes up and down the skyline like a trolley cart. The chokers which are used to hook the logs are attached to the end of the mainline. Logs are then hooked with the chokers and the yarder operator engages the mainline drum.

The logs are pulled to the center of the strip and then up towards the carriage until the mainline stop hits the carriage. At this point, the carriage releases and the drag is then pulled up the hill with at least the front of the logs off the ground. This minimizes soil disturbance and compaction on the ground. Line machines and their hardy crews are able to log on very steep and rugged terrain.
In today's logging industry where much is mechanical, line logging is utilized when the ground is too steep for mechanized equipment. The work is done by hand with trees felled by a hand sawyer, hooked by a choker or "hooker", and unhooked by the landing man or "chaser". It’s labor intensive but is still a viable and efficient logging method that is important for the timber industry in Montana. Line machines can safely log ground that couldn't be harvested other than by helicopter. If there is an accessible road at the top of a patch of commercial timber, a line machine can get the logs out.
Helicopter Logging
This is when the going gets tough. If the ground is too steep for conventional or mechanical logging, or not accessible by a line machine, it’s time to bring in the helicopter. With helicopter logging, trees are felled and generally bucked into logs on the strip. There are several reasons for this. One: helicopters are expensive to operate so it doesn’t make sense to fly anything other than processed logs. Two: many trees are too heavy to be “whole tree” flown.
After the sawyers have fallen and bucked the trees, chocker-setters hike into the strip. Often, there are a dozen chocker-setters working hard to keep one helicopter busy. The helicopter is fitted with a static line with an electronic latch that is operated by the pilot. Once the chocker-setter has a drag hooked, the pilot hovers over him and the chocker- setter hooks up his drag. They must accurately estimate the weight of the logs so the helicopter is neither overloaded nor under loaded. The pilot then lifts the logs and flies them to the landing where the knot bumper or processor cleans them up.
Helicopter logging is useful when minimal ground impact is required. Because the logs are lifted straight up from where they are felled, soil disturbance in the area is minimal. From the large helicopters that can lift a 20,000 pound drag, to the smaller Hueys, helicopter logging fills a unique and important niche in Montana’s timber industry.